














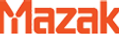










Post-Processing Software
Supported CAD/CAM systems;
-
CATIA
-
Siemens NX
-
Solidcam
-
Cimatron
-
Mastercam
-
Tebis
-
Powermill
-
Camworks
-
ProEngineer
-
HyperMill
-
HSMWorks
-
Inventer HSM
CanikSoft Post-Processing software converts the Cutter Location Data (CL Data) which comes from a CAD-CAM system to the specific machine tool commands (G-Code).
CanikSoft Post-Processor software supports machines 5 axis to 9 axis. Also it is possible to generate post processors for all kind of CNC machines.
It is possible to try CanikSoft Post-Processor software before buying it. Just inform us the machine type and the CAD CAM system used. Use it 30 days free then decide to buy or not.
Some futures of CanikSoft Post-Processing software;
-
Unique Interface: Provides unique interface for all CAM softwares.
-
Fast Post: You do not have to see the CanikSoft Post-Processing user interface. When you click Post Process button of your CAM software CanikSoft Post-Processing software automatically reads the CL Data and converts it to G-Code.
-
Multi File Post-Processing: It is possible to Post-Process multiple files by just one click. Just select files and press Enter key. CanikSoft PostProcessor converts all CLData/APT files to G-Code and you save time.
-
Post Machine Control: If you have several machines similiar, CanikSoft Post-Processing software prevents to run G-Code on machine which belongs to other machine. If you run the G-Code on wrong machine the machine gives alarm.
-
CL Data Control: CanikSoft Post-Processing checks the CL Data during postprocessing software. If you forgot to enter the spindle speed of an operation CanikSoft Post-Processing software generates a warning. However it is possible to correct this kind of informations in software. (Spindle speed, feedrate, tool number etc). Also it gives an option to use variables on tool numbers, spindle speeds and feedrates. So operator can easly correct them on machine side.
-
Operation Type Determination: CanikSoft Post-Processing software automatically detects the operation types and generates regarding commands to the machine side. For example for simultaneous operations it unclamps the rotary axes and activates TCP if machine has.
-
Safe Approach: CanikSoft Post-Processing software uses special algorithms for first move of every operations depending on the machine kinematics type. So it provides safe way to approach the part for every operations. If there is no move on rotary axes for an operation it checks the last position of previous operation and it decides to move X,Y first then Z or move Z first then X and Y.
-
Rough-Finish Mode Control: CanikSoft Post-Processing software automatically detects the roughing and finishing operations and generates machine specific commands like tolerances.
-
Safe Approach On Angle Change: If the rotary axes will rotate for the new operation the software automatically moves tool to safe place. After the rotation it uses safe approach algorithms depending on machine kinematics,
-
Singularity: If the tool orientation becomes paralel with the C axis it knowns as singularity. In this situation it is possible use every positions of the C axis. CanikSoft Post-Processing software makes possible to use of singularity,
-
Auto Limit Correction: If an operation exceeds the machine limits the software automatically can find the C axis position (if possible) which allows the machine the operation in limits. The software reports the new C axis position to the user.
-
Angular Head Support: It is possible to use angular head attachments in CanikSoft Post-Processing software including 5 axis simultaneous operations using right angular heads,
-
Multi Axis Drilling: In multi axis drilling operations it is possible to drill all holes in one operation. The tool does not move to the reference position for every drill positions and it saves time,
-
User Defined Parameters: CanikSoft Post-Processing software allows creating the user defined parameters. These parametrs can be directly used in G-Code macro. It gives flexibility to customise the software for specific needs. The software remembers the last values for every parameters,
-
Convert Circle, Helix, Cycles: CanikSoft Post-Processing software can convert the circular, helical or cycle commands to the linear movements. If the machine does not support these functions CanikSoft Post-Processing software automatically converts these moves,
-
Correcting Circular Moves: CanikSoft Post-Processing software automatically corrects the too small or too big circular moves which can be problem on machine tool side,
-
Alternative Angles: In 5 axis machines every operation has two solutions/alternatives. The CanikSoft Post-Processing software can automatically decide which to use, however the user has ability control the solution,
-
Lock Axis: In singular operations CanikSoft Post-Processing software allows to lock any of X or Y axis to stay in machine limits. CanikSoft Post-Processing software moves the C axis insteed.
-
Auto Selecting Alternative Angles: CanikSoft Post-Processing software can choose the best alternative solution on simultaneous operations. It chooses the shortest distance,
-
Retract & Re-Engage: In simultaneous operations if the rotary axes limits exceeds the software has a special algorithm to safe and fast switching to other solution depending on machine kinematics.
-
C Axis Optimisation: In simultaneous operations the singular tool orientations causes quick turns on C axis. CanikSoft Post-Processing software automatically catchs it and optimizes the C axis positions for singularity,
-
Linearization: For the machines does not have TCP option on simultaneous operations the tool tip point can leave the toolpath because of combination of two rotary movements. CanikSoft Post-Processing software automatically finds it and adds additional points to the toolpath to stay in tolerances,
-
Maximum Angle Change: In simultaneous operations the quick turns of the rotary axes can damage the tool, part or the machine. CanikSoft Post-Processing software automatically finds these kind of problems and optimizes the toolpath by adding additional points to the toolpath,
-
Tool Length Control On Machine Side: If the tool needs to be long for an operation because of the machine collision, CanikSoft Post-Processing software can output special macros to stop machine if the tool length is small then given,
Rotating The Table
If the tool orientation becomes paralell with C axis direction vector it knowns as singularity.
The user can free to rotate the table on singular operations to stay in machine linear axes limits.
Auto Rotate Table
If a singular operation exceeds linear axis limits it is possible to rotate the table to stay in machine limits. Alternatively the post-processing software can automatically find the table position to stay in machine limits. If this option is activated the post software tries every positions and informs the user if it finds a solution in machine limits.
Locking Linear Axis
If a singular operation exceeds linear axis limits it is possible to lock X or Y axis and rotate the table insteed. The post software calculates C axis positions for every motion to compensate the linear axis position. Also it adds additional toolpath points to stay on toolpath.
Alternative Solution
In 5 axis machines every operation has two solutions/alternatives. The CanikSoft Post-Processing software can automatically decide which to use, however the user has ability control the solution
Alternative Solution Simultaneous
In simultaneous operations there are two options for alternative solutions. Start angle selection and allowing the other solution. Start angle can be selected by user or can be used defaults. If the user allows the solution switching the software choose the nearest solution makes minimum movements. If rotary limits exceeds it uses the retract-reengage algorithms